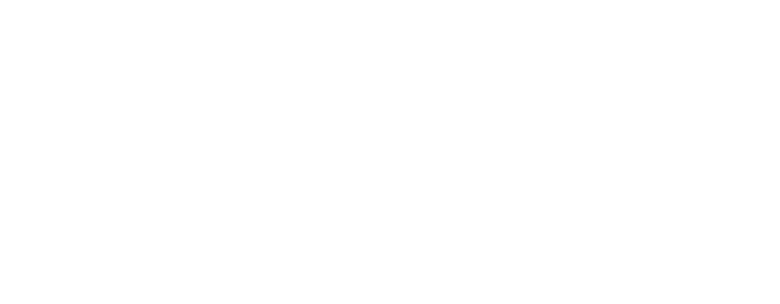
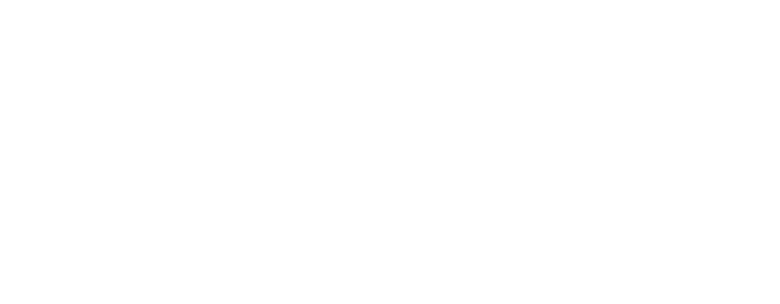
Statistics show interesting facts – for example, in the US people on average spend 4.3 years in their cars over the course of their lives [source: Distractify]. Another study shows that people spend 15 hours per week in their vehicles on average [source: Arbitron]. Reducing this time is the task of various industries, ranging from spatial planning to politics and many others. But making the time spent in your car more useful and comfortable is something where also the field of in-wheel motor technology development can help.
Current powertrain architectures offer complicated solutions and energy inefficiencies. Internal Combustion Engines (ICE) are limited with Carnot cycle and construction material’s thermal stability. Number of moving parts is above 200 and the complete powertrain bill of material includes more than 1500 parts.
Automotive sector has been looking in the last decades for incremental improvements, however much more can be done and some innovative companies already offer radical changes in powertrain technology.
How is that possible?
First, let’s see the flat battery design as demonstrated by Tesla Inc. As one of their first achievements, Elon Musk and his team developed a battery pack for a SmartTM and demonstrated it to Daimler back in 2009, which resulted in their first multimillion dollar deal. The flat battery design fits perfectly with the vision of autonomous driving as the passenger and cargo space is increased while the center of gravity is kept low, providing better handling. In combination with the apparent silence of electric vehicles, additional comfort and driving experience can be offered with this solution.
Technology giants such as Google, Tesla and Apple are envisioning the future car to be autonomous or self driving. Elaphe is aware of the opportunities in this area and is preparing the propulsion electronics to be fully compatible with autonomous driving technologies. However, to make the in-wheel architecture possible, compact high-performance in-wheel motors are required. The M700 motor with 700 Nm of peak torque and just 20 kg of additional weight is one of the possible solutions.
[Featured study car scheme was obtained at: http://www.product-reviews.net/]